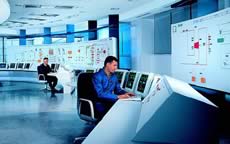
Системи АСУ ТП, АСУП, SCADA и АСДУ
Автоматизовані системи управління технологічними процесами (АСУТП) та системи диспетчерського управління (АСДУ) енергетичних та промислових підприємств є обов'язковою умовою їх функціонування, нормальної експлуатації, запобігання аваріям та забезпечення високої ефективності в цих ринкових умовах.
Сучасні АСУТП, що розробляються із застосуванням програмованих мікропроцесорних контролерів, крім забезпечення всіх необхідних функцій, дозволяють мати широкий вибір додаткових можливостей, забезпечують високий рівень надійності, мають високорозвинену гнучку структуру і високоефективний людино-машинний інтерфейс. Оснащення підприємства такої АСУТП може бути виконане двома шляхами: 1-й - проектування та встановлення АСУТП виконується безпосередньо під час будівництва нового підприємства; 2-й – реконструкція існуючих АСУТП із заміною основного обладнання – вимірювальних пристроїв, виконавчих механізмів та логічної частини АСУТП.
Єдиним шляхом забезпечення сучасних вимог до виробництва, енергозабезпечення та енергозбереження є впровадження сучасних АСУТП на мікропроцесорній базі з використанням високоточних та надійних датчиків та виконавчих механізмів.
АСУТП розробляються як розподілені інформаційно-керуючі людино-машинні системи, розраховані на тривале функціонування в реальному масштабі часу та призначені для автоматизованого управління будь-яким технологічним обладнанням, яке є об'єктом управління АСУТП.
Основними перевагами при впровадженні запропонованих нами АСУ ТП є:
![]() |
- підвищення надійності роботи обладнання; зниження ризику важких аварій;
- забезпечення автоматизованого ефективного управління технологічними процесами в нормальних, перехідних та передаварійних режимах роботи, вироблення продукції заданої якості та кількості;
- захист обладнання та персоналу при загрозі аварії;
- покращення умов праці експлуатаційного персоналу;
- своєчасне подання оперативному персоналу достовірної інформації про перебіг технологічного процесу, стан обладнання та технологічних засобів управління;
- забезпечення персоналу ретроспективною інформацією у повному обсязі для аналізу, оптимізації та планування роботи обладнання, а також його ремонту.
При створенні АСУТП враховуються критерії ефективності АСУТП, які є кількісним виразом наступних показників:
- витрат на ремонт обладнання, що визначаються надійністю обладнання та ефективністю планування його ремонтів;
- витрат на технічні засоби АСУТП, що визначаються темпами введення та освоєння АСУТП;
- зниження кількості обладнання АСУТП та кабелю.
Високі показники функціонування АСУТП досягаються завдяки застосуванню найсучасніших програмних засобів, що забезпечують:
- реалізацію особливо складних алгоритмів управління та регулювання;
- оптимальний зв'язок (інтерфейс) «людина-машина»;
- розширені інформаційні функції АСУТП;
- адекватну діагностику технологічного обладнання та засобів АСУТП;
- високу живучість та надійність системи при відмови її окремих елементів;
- спрощення керування технологічним обладнанням.
Відмінними рисами наших систем є:
- застосування досвіду оригінальних розробок та досліджень у частині створення перешкодозахищених інформаційно-вимірювальних каналів АСУТП об'єктів, що гарантують відсутність збоїв у роботі АСУТП через електромагнітні перешкоди;
- обов'язковий економічний аналіз шляхів оптимізації проектних рішень при створенні АСУ ТП та зниження витрат Замовника на постачання електрообладнання та матеріалів;
- досвід реконструкції релейно-контактних систем управління (у т. ч. – виконаних на вітчизняних апаратних засобах) із заміною їх на мікропроцесорні з мінімальними витратами та максимальною ефективністю (включаючи аналіз використання існуючих кабельних зв'язків);
- обов'язкове впровадження енергозберігаючих технологій шляхом широкого застосування:
- пристроїв плавного пуску та частотного регулювання при постачанні нових електроприводів та для реконструкції існуючих напругою 0,4 кВ та 6 (10) кВ;
- пристроїв компенсації реактивної потужності ;
- Остаточне рішення щодо конфігурації АСУТП приймається нами лише після ретельного безпосереднього обстеження, вивчення та докладного аналізу особливостей об'єкта - для конкретних умов роботи нами приймається найбільш оптимальне рішення.
- комплексне проектування, постачання обладнання та введення в експлуатацію з одних рук.
Основна відмінність наших проектів – економічно прорахована комбінація застосування високоякісного обладнання зарубіжних виробників у поєднанні з перевіреним вітчизняним обладнанням, що забезпечує максимальну оптимізацію витрат на систему автоматизації.
В результаті впровадження АСУТП досягаються:
![]() |
- стійка безаварійна робота технологічного устаткування;
- підвищення рівня експлуатації та надійності систем управління;
- суттєве покращення всіх економічних показників роботи об'єкта;
- збільшення терміну служби обладнання та зменшення трудових та фінансових витрат на його ремонт;
- суттєве підвищення показників енергозбереження;
- забезпечення вимог вітчизняних та міжнародних стандартів до виробництва.
Структура АСУТП об'єкта представляє трирівневу функціонально і територіально розподілену багатомашинну систему і включає:
- загальнооб'єктний рівень контролю, що реалізує функції управління загальнооб'єктними системами та відображення інформації (мікропроцесорні засоби);
- агрегатний верхній рівень, що реалізує функції оперативного контролю стану та дистанційного керування технологічним обладнанням, а також реєстрація, протоколювання та архівування інформації (мікропроцесорні засоби);
- агрегатний нижній рівень, що реалізує функції збору та попередньої обробки інформації, автоматичного управління виконавчими органами (мікропроцесорні засоби, первинні датчики та виконавчі механізми та кабелі між ними).
Усі рівні об'єднані локальною обчислювальною мережею (кручена пара, оптоволокно). Нижній рівень управління АСУТП об'єкта становлять локальні системи автоматизованого управління (ЛСУ), побудовані з урахуванням однієї (кілька) шаф мікропроцесорних контролерів і призначені реалізації функцій контролю та управління устаткуванням межах виділених технологічних функціональних зон.
Технічними засобами рівнів є:
- для загальнооб'єктного рівня та агрегатного верхнього рівня – загальнопромислові персональні комп'ютери, мережеві концентратори та засоби відображення колективного користування (супер-монітори чи проекційні екрани);
- для нижнього агрегатного рівня:
- ЛСУ – високонадійні та гнучко-конфігуровані промислові контролери модульного виконання, інтегровані з відповідними модулями вводу/виводу;
- датчики та виконавчі механізми – вимірювальні перетворювачі тиску (різниці тисків), температури, хімічного контролю та газоаналізу, спеціалізовані датчики (контроль наявності полум'я, переміщення, вологості тощо), запірна та регулююча арматура, приводи агрегатів (у тому числі з пристроями плавного пуску та частотного регулювання).
Комплектація нижнього агрегатного рівня проводиться обладнанням SIEMENS, OMRON, ENDRESS+HAUSER, Unitronics, Pepperl+Fuchs, Danfoss, Gessmann, ОВЕН та іншим, та технологічним обладнанням: компресори ASPERA, насоси KSB , HILGE, PROMINENT та ін.
Диспетчеризація SCADA
![]() |
ТОВ «Техноелектро» здійснює системну інтеграцію систем диспетчеризації та моніторингу технологічних процесів (SCADA-системи). Будь-яке промислове обладнання та інженерні системи можуть працювати під контролем SCADA-систем:
- Технологічні процеси;
- Інженерні системи об'єктів нерухомості;
- Обладнання: насоси, вентилятори, компресори, приводи тощо.
Ключовими перевагами використання диспетчеризації є:
- Можливість збору, проведення первинної обробки та формування інформаційних архівів включають дані про параметри технологічних процесів і актуальний стан обладнання.
- Виведення у графічному вигляді або мнемосхем інформаційних звітів про поточний стан параметрів технологічних процесів на екрани робочих станцій (ПК).
- Здійснення віддаленого доступу в режимі реального часу або використовуючи задані часові інтервали до технологічних параметрів, у тому числі надання віддаленого доступу до пристроїв нижнього рівня та сигналізаційних систем.
- Відображення звітів у графічному вигляді поточних значень заданих параметрів.
- Здатність виявляти та пропонувати рішення для якнайшвидшого усунення можливих аварійних ситуацій.
- Конфігуровані інструменти, для оперативного та якнайшвидшого визначення характеру та подальшу локалізацію аварійних сигналів, з підтримкою функцій швидкого аналізу та реагування на ситуації аварійного характеру.
- Використання будь-яких можливих індикаційних екранів, крім комп'ютерних моніторів, для виведення повідомлень, як технологічних, і аварійних.
- Архівування та хронологізація історії застосованих змін до параметрів технологічних процесів.
- Програмні комплекси поєднують у собі високошвидкісні системи збору даних, що надає роботу з хронологічними послідовностями, дозволяючи проводити оптимізацію процесів пошуку та подальшого зберігання даних.
- Забезпечення операторів та обслуговуючого персоналу віддаленим доступом до управління технологічними процесами.
- Миттєве надання бази даних про застосовувані параметри для технологічних процесів з подальшим використанням їх у системах управління підприємством.
- Широкий асортимент різноманітних режимів пошуку інформації, що дозволяє швидше складати звіти.
- Можливість швидкої генерації та надання для перегляду звітів щодо історичних змін застосовуваних параметрів для технологічних процесів.
- Значно спрощене створення багаторівневих, розподільчих систем, які забезпечують безперервність робочих процесів Вашого бізнесу.
- Технології автентифікації, що надають безпеку та забезпечують більш гнучку роботу операторів, що знижують ризики, пов'язані з несанкціонованими змінами в системі.
- Миттєва оптимізація роботи всіх задіяних виробничих систем і помітне скорочення ресурсів, що витрачаються, на підтримку їх у постійному робочому стані.
Етапи впровадження систем диспетчеризації, SCADA-систем
![]() |
SCADA-системами можуть бути як локальні системи диспетчеризації, так і багаторівневі територіально-розподілені системи. Створення проекту починається з формування узгодженого із замовником технічного завдання, це перший етап, який готується при обстеженні об'єкта та проектуванні техніко-комерційної пропозиції. Наші фахівці пропонують професійно та швидко впровадити SCADA-системи «під ключ», що означає виконання всіх необхідних робіт: починаючи з підготовки контролерів, їх програмування, закінчуючи проведенням пуско-налагоджувальних робіт та здачею в експлуатацію готових систем після належного відповідного тестування. Завдяки широкому застосуванню SCADA-систем на потужностях багатьох підприємств на сьогоднішній день існує великий вибір рішень, що надає замовнику гігантський простір для формування відповідної конфігурації системи диспетчеризації.
Проектування систем на основі SCADA систем включає наступні етапи:
- Проектування рівня контрольно-вимірювальних приладів та «польового» обладнання. Цей етап являє собою проектну розробку функціональної схеми автоматизації об'єкта та вирішення пов'язаних з цим питань: як організувати найкращий варіант, що дозволяє здійснювати віддалений доступ, визначення необхідних типів датчиків, їх кінцевого розташування (місць встановлення) в системі та виконавчі механізми, розробку структурної схеми комплексу технічних. засобів, електричної принципової схеми шафи автоматики, планування траси та схеми зовнішньої проводки.
- Проектування системи збору та обробки інформації, управління виконавчим механізмами. Реалізація даного етапу передбачає: вибір відповідних типів та складу контролерів, проектування алгоритмів функціонування та подальше програмування контролерів. Особливу увагу слід приділяти програмній реалізації, що використувується в контролерах, а також керуючих та виконавчих пристроях, оскільки це впливає на майбутню стабільність роботи та стійкість до відмови автоматизованої системи.
- Проектування операторських пунктів та мереж. Цей етап являє собою логічну побудову та створення проекту найкращого варіанту мережі віддаленого доступу до різних параметрів системи, що враховує створення робочих місць для операторів, формування та розробку прикладного програмного середовища для операторських станцій, мережного обладнання та промислових серверів.
При створенні автоматизованої системи будь-якої складності нашими спеціалістами використовуються лише найякісніші та найнадійніші комплектуючі від найвідоміших виробників – Siemens, ABB, Schneider Electric, General Electric, Eaton, Danfoss, Omron та багатьох інших.
Управління виробництвом
ТОВ «Техноелектро» здійснює впровадження та планове обслуговування автоматизованих систем управління виробництвом (АСУП), так званий MES-рівень (Manufacturing Execution System).
Задіявши інформацію рівнів контролю та планування, MES-системи контролюють поточну виробничу діяльність відповідно до запитів, вимог технологічної та конструкторської документації, що надходять, актуальний стан обладнання та мають орієнтованість на максимізацію ефективності та мінімізацію вартості виконуваних виробничих процесів.
Функції MES-систем:
![]() |
- Моніторинг станів та розподіл ресурсів. Управління ресурсами виробництва: матеріалами, персоналом, технологічним обладнанням, інструментами, документацією та методиками робіт.
- Детальне та оперативне планування. Ведення виробничих розкладів, що ґрунтується на пріоритетах, характеристиках, атрибутах та способах, що залежать від специфіки виробів та технологій виробництва.
- Диспетчеризація виробництва. Контролює потоки деталей, що виготовляються за серіями, партіями, замовленнями та операціями, використовуючи систему робочих нарядів.
- Збір та зберігання інформації. Організація взаємодії інформаційних підсистем для отримання, упорядкування та транспортування керуючих та технологічних даних, що мають оборот у виробничому середовищі підприємства.
- Управління документами. Облік змісту та проходження документів, що супроводжують виготовлення продукції, ведення звітної та планової документації.
- Організація персоналу. Надання можливості щохвилинного керування персоналом.
- Контроль за якістю продукції. Аналізація інформації про вимірювання якості продукції заснованої на інформації, що надходить фахівцям у режимі реального часу, з виробничих рівнів, забезпечення потрібного рівня якості, виявлення критичних точок та проблем, яким слід приділити особливу увагу.
- Контроль виробничих процесів. Ведення моніторингу виробничих процесів, автоматизоване коригування чи діалогова підтримка за втручання оператора.
- Аналіз продуктивності. Формування докладних звітів про досягнуті результати виробничих операцій. Порівняння фактичних та планових показників.
- Управління ремонтом та техобслуговуванням. Організація планового технічного обслуговування та оперативне проведення ремонтних робіт для підтримки експлуатаційної придатності обладнання та інструментів.
- Веде історію продукту. Графічне відображення інформації про місце та час виконаних робіт з кожного продукту. Можливість включення до звіту інформації: про партійні та серійні номери, виробничі корекції, виконавців, технологічні маршрути, матеріали, комплектуючі, поточні умови виробництва та інші дані.
Переваги інтеграції АСУП (MES) для Вашого підприємства
![]() |
Операції, які виконують MES-системи, можливо інтегрувати з іншими діючими системами управління підприємством, наприклад: SCM (Планування Ланцюгів Поставок), ERP (Планування Ресурсів Підприємства), SSM (Продажі та Управління Сервісом) та АСУТП (Автоматизовані Системи Управління Технологічними Процесами). Це дозволяє забезпечити своєчасний та всеосяжний контроль критичних виробничих процесів:
- Додаткова вартість продукції задається у виробничих зонах (дільницях, цехах), тому реальну віддачу надають інвестиції в підвищення ефективної складової виробничих процесів.
- Надання своєчасної та достовірної інформації, важливої для ухвалення правильних рішень фахівців, що знаходиться безпосередньо у виробничих зонах.
- Оптимізоване управління технологічними процесами сприяє реальним змінам фінансових показників Вашого підприємства.
- Діючі виробничі зони характеризують конкурентоспроможність Вашого підприємства, його можливості для моментальної переналагодження змінюваних вимог з боку споживача.
- Ефективність та прибутковість Вашого підприємства залежить від персоналу, що працює у виробничих зонах, можливості якого багаторазово зростають при використанні систем типу MES.
- Під час виявлення позаштатних чи критичних ситуацій у виробничих зонах системи типу MES моментально проводять аналіз інформації та оперативно пропонують коригуючий курс на вирішення проблеми.